Auf einen Blick
Der Kunde wünschte eine Maschine mit vier unabhängigen angetriebenen Linearachsen mit einer maximalen Hubkraft von je 15'000 N auf drei Achsen, wobei die vierte Achse eine Spezialachse mit deutlich anderen Anforderungen war. Gewisse Achsen sollten mit je zwei Kraftsensoren ausgestattet sein, um die effektiv anliegende Druck-/Zugkraft genau messen zu können sowie Endschaltern für eine präzise Referenzierung.
Da die Maschine auch künftig in den USA vertrieben werden soll, war eine dezentrale Motorsteuerung mit 48 VDC gewünscht.
Konzept & Aufgaben
Da bereits eine Vorgängermaschine vorhanden war, analysierten wir zunächst deren Merkmale und Hardwareprobleme und führten eine Risikoanalyse durch, um sicherzustellen, dass alle Spezifikationen festgehalten waren. Da die Entwicklungszeit kurz und die Maschine komplex war, arbeiteten wir mit einem externen Konstrukteur zusammen, der vom Kunden gestellt wurde. Die Verantwortung für die Genehmigung der mechanischen Umsetzung, der Antriebstechnik und alle elektrotechnischen Aufgaben lag bei uns.
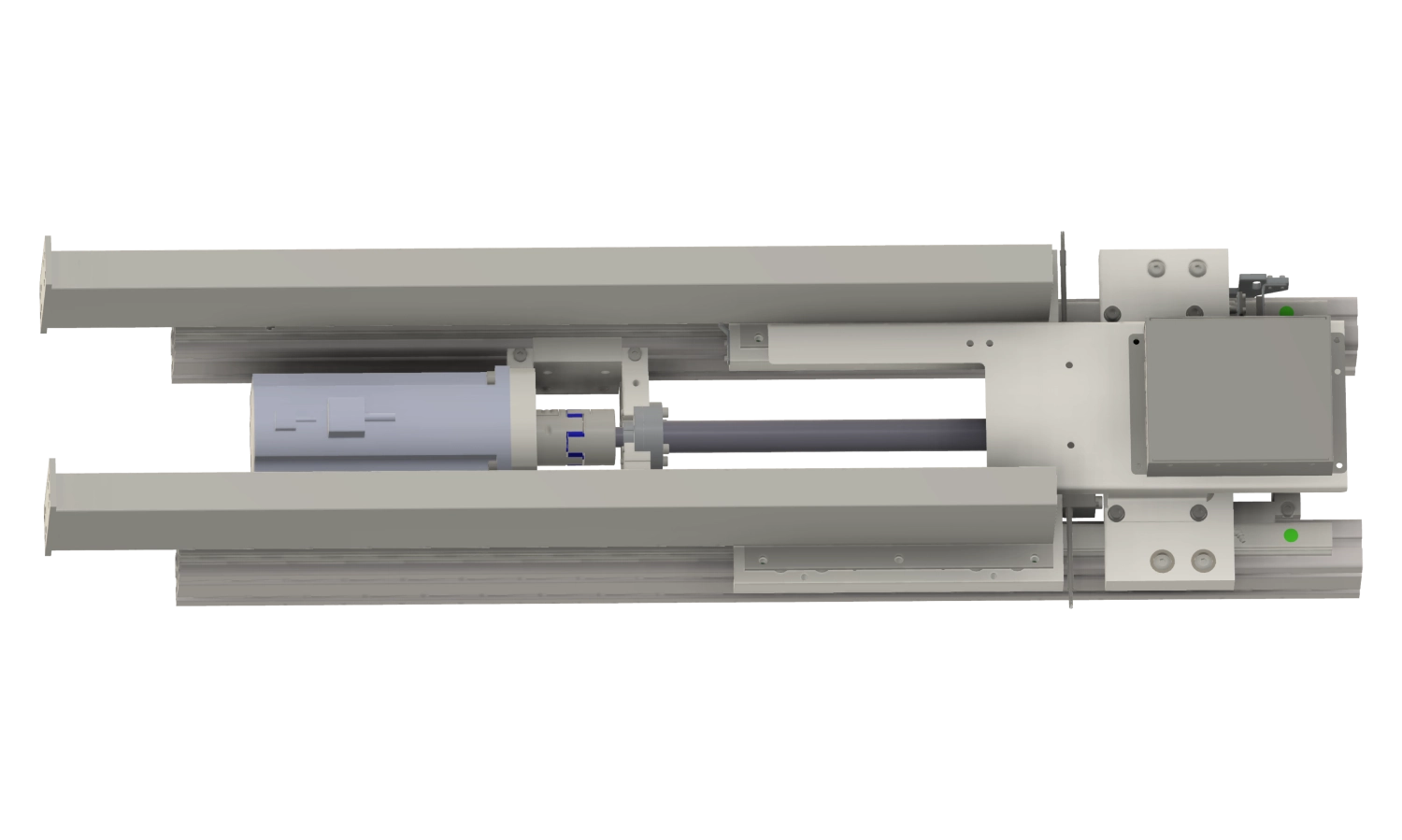
technischer Ansatz
Auf Grund der grossen Kräfte wurden drei Achsen mit Kugelumlaufgewindetriebe (KGT) aufgebaut und die vierte, sehr kurze Achse mit kleinen Kräften mit einem Trapezgewinde mit automatischem Schmierstoffgeber. Um Produktionskosten zu reduzieren, musste die Mechanik Fertigungstoleranzen auszugleichen vermögen, unter anderem wurden die Schlitten schwimmend gelagert.
Wir durften für den Auftrag mehrere Elektronik-Platinen pro Gerät designen und produzieren. Unsere X1-Motorsteuerung wurde spezifisch angepasst und vordefinierte Verhaltensweisen direkt einprogrammiert. Jede Achse wurde mit einer Elektrobox (s. Bild oben) ausgestattet, so dass nur CAN und die Versorgung auf die Achsen gezogen werden musste. Peripherie wie die Kraftsensoren werden direkt in die jeweilige Box eingesteckt; Bremschopper schützen vor Überspannung im Zwischenkreis beim Abbremsen.
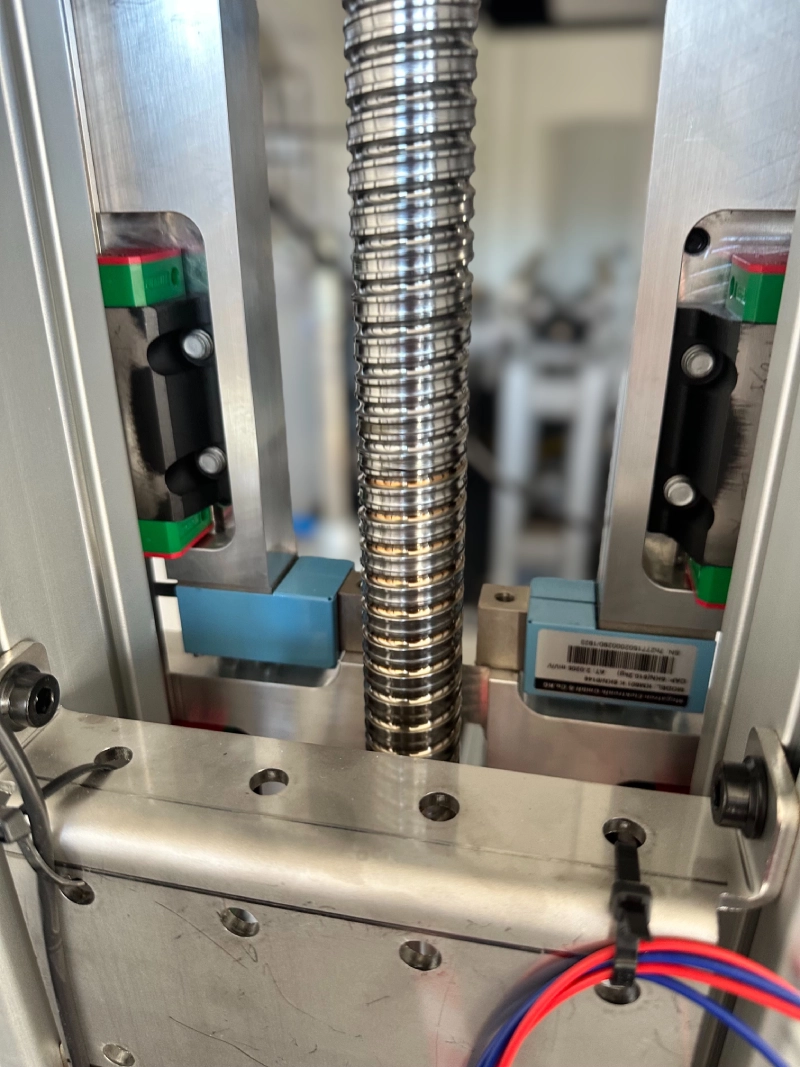
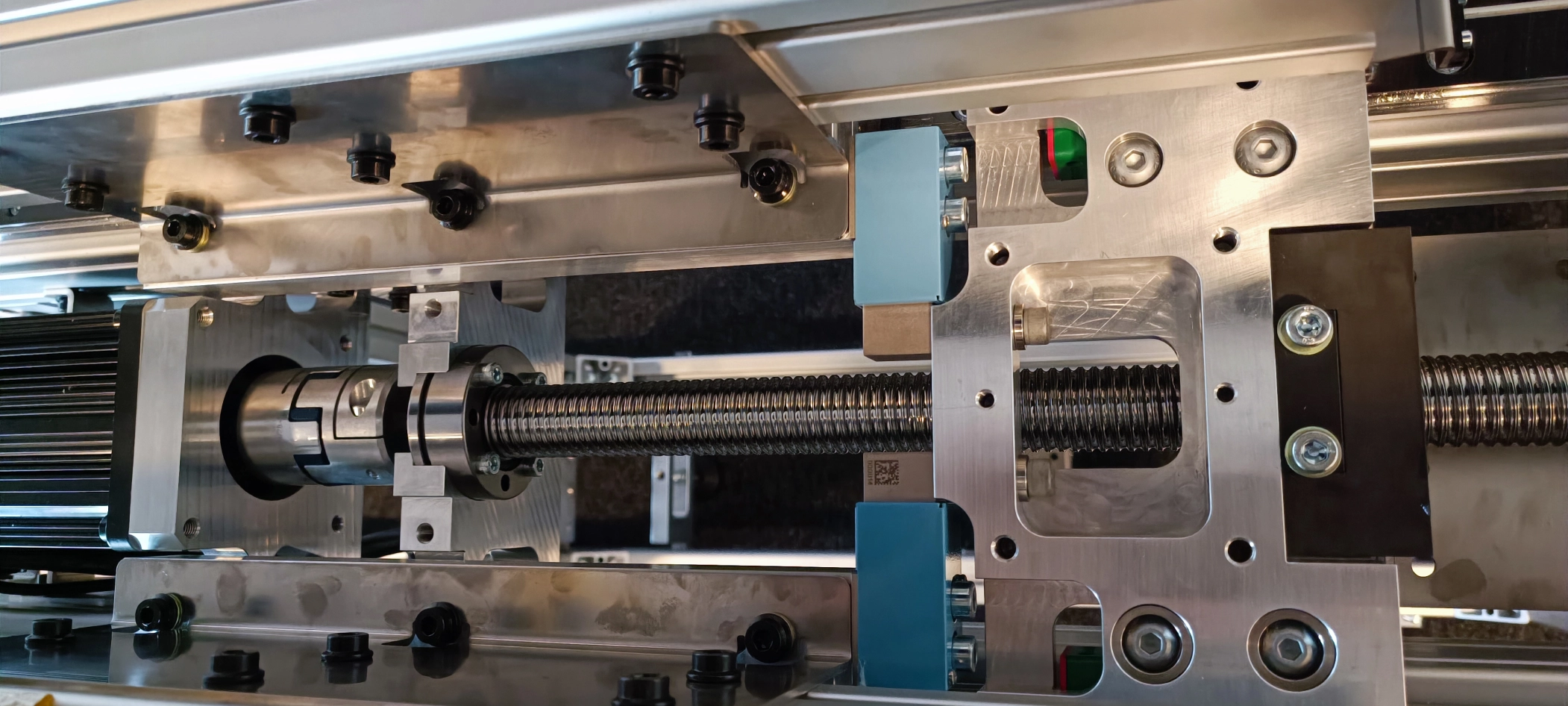
Testen
Um früh Erkenntnisse zu sammeln, wurden die einzelnen Teilkomponenten unabhängig voneinander getestet. Es wurde ein Dev-Kit aufgebaut bestehend aus einer Achse, Endschaltern sowie den Sensorenum sowohl die Firmware als auch die Software zur Ansteuerung der Maschine zu entwickeln und zu testen.
Vor den ersten Prototypen wurde ein Funktionsmuster erstellt. Mittels Pneumatik-Zylindern wurde die Gegenkraft generiert und ein Dauertest von 100'000 Zyklen umgesetzt. Anhand der hohen Datenrate von bis zu 300 Messpunkten pro Sekunde (doppelte Kraftmessung, Position, Geschwindigkeit und Strom) konnten kleinste Veränderungen wie eine Zunahme der Reibung noch festgestellt werden und mechanische Folgeschäden vermieden werden. Die Testergebnisse flossen in die weitere mechanische Entwicklung ein.
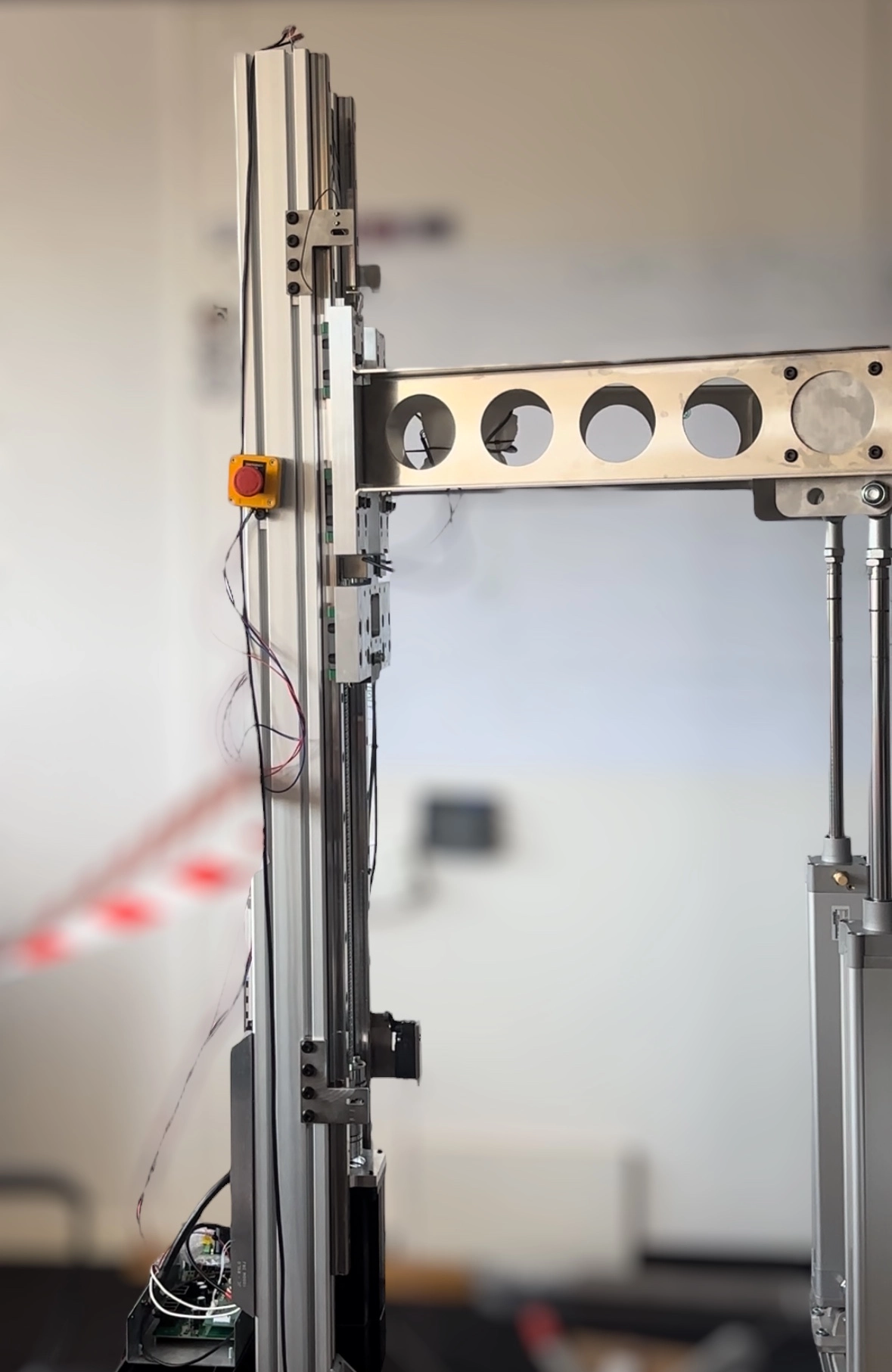
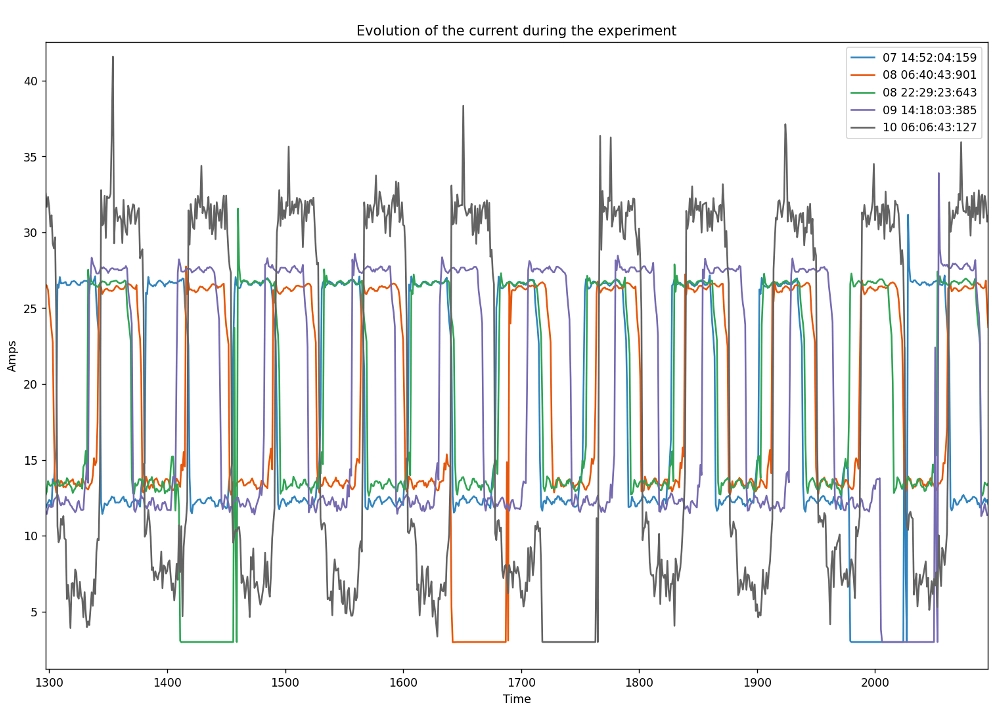